This project focuses on integrated kitchen appliances, achieving not only rapid and stable stamping loading and unloading through robots but also flexible production lines via mold-changing trolleys. It reduces equipment investment, conserves production space, and resolves issues of time-consuming and labor-intensive manual mold changes.
Overall Improvement Plan
By integrating a multi-functional servo feeder at the first station for dual-material detection and oil application, combined with high-payload robots for loading and unloading in the middle, we have automated the general stamping process for integrated kitchen appliances. Simultaneously, we have developed a rapid mold-changing system that is highly synchronized and integrated with the production line, including intelligent rapid mold-changing trolleys, quick-change robot arms, and fixture quick-change devices. This system enhances the compatibility and versatility of the production line, significantly reduces equipment investment, meets the demand for flexible and rapid model changes, and greatly improves equipment utilization.
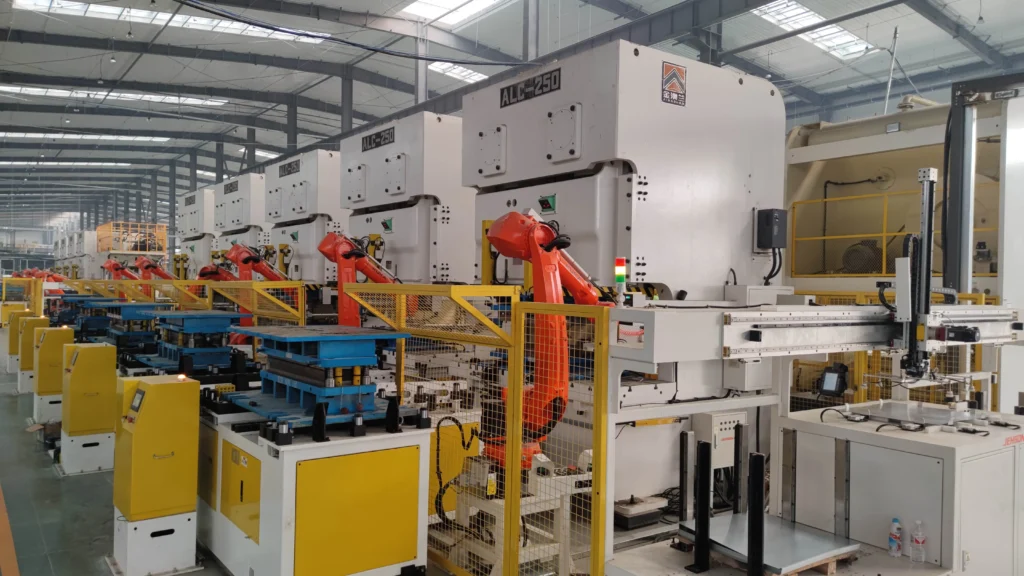
Innovative Processes
Innovative Process 1: Intelligent Rapid Mold-Changing System Technology
The mold-changing trolley is developed through the integration of dual-station trolleys, mold push-pull systems, flip transition tables, ground tracks, mold lifters, upper/lower clamping devices, and electric control systems. Meanwhile, the robot arms and fixtures employ quick-change devices, enabling rapid insertion and extraction. These elements are synchronously controlled with the mold-changing trolley and robot production line through a master control console.
Innovative Process 2: Multi-Machine Collaborative Control System Technology Supporting EtherCAT and ModbusTCP Bidirectional Communication Protocols
Utilizing a central control system that coordinates servo sheet feeders, stamping robots, and rapid mold-changing trolleys, and equipped with Ethernet interfaces, this technology supports EtherCAT and ModbusTCP bidirectional communication protocols. It connects the robot production line and the entire workshop to enterprise information systems such as MES, ERP, and PLM, enabling digitalized and intelligent production in the Industry 4.0 environment for integrated kitchen appliances.