Slide rails, also known as guide rails or slides, are hardware connecting components fixed to the carcass of furniture, allowing drawers or cabinet panels to move in and out. They are widely used in cabinets, furniture, filing cabinets, bathroom cabinets, and other wooden and steel drawers. Taking drawers as an example, the typical drawer slide is a concealed three-section slide rail, consisting of a middle rail, a movable rail (“inner rail”), and a fixed rail (“outer rail”). In this article, we will use “slide rails” as an example to showcase how Jehson robots, with their exceptional mold technology and continuous iteration and upgrading of existing punching manipulator technology, maximize the benefits of technical transformations for customers.
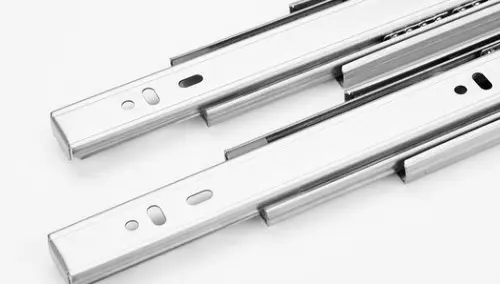
The manufacturing process of slide rails involves six steps: tongue cutting, punching, counterboring, bending, ribbing, and tongue cutting again. To increase production output, Jehson robots, relying on the strength of the Kaishuo Mold Group, design all molds with a 1-out-2 structure (i.e., left and right products are punched simultaneously in the mold). The guide pillars of all molds are fixed on the upper mold, and the guide bushes are fixed on the lower mold, allowing for quick mold changes. Additionally, all molds are equipped with cylinder mold-changing devices to meet the product mold-changing needs for different lengths, fundamentally achieving flexibility in the line.
Next, let’s take the arm-swinging intelligent punching robot connection solution as an example. By adopting the self-developed Jehson arm-swinging intelligent punching robot, it achieves four-axis high-speed linkage for arm lifting, swinging, stretching, and gripper rotation, replacing imports. At the same time, a “double-material” gripper system is developed to flexibly and accurately grab and release two workpieces, thereby increasing overall production efficiency and saving equipment investment. With this setup, the maximum efficiency can reach 12 strokes per minute (when the punch press SPM is 40), meaning the production output per minute of the line can reach 24 pieces (since the mold has a 1-out-2 structure).
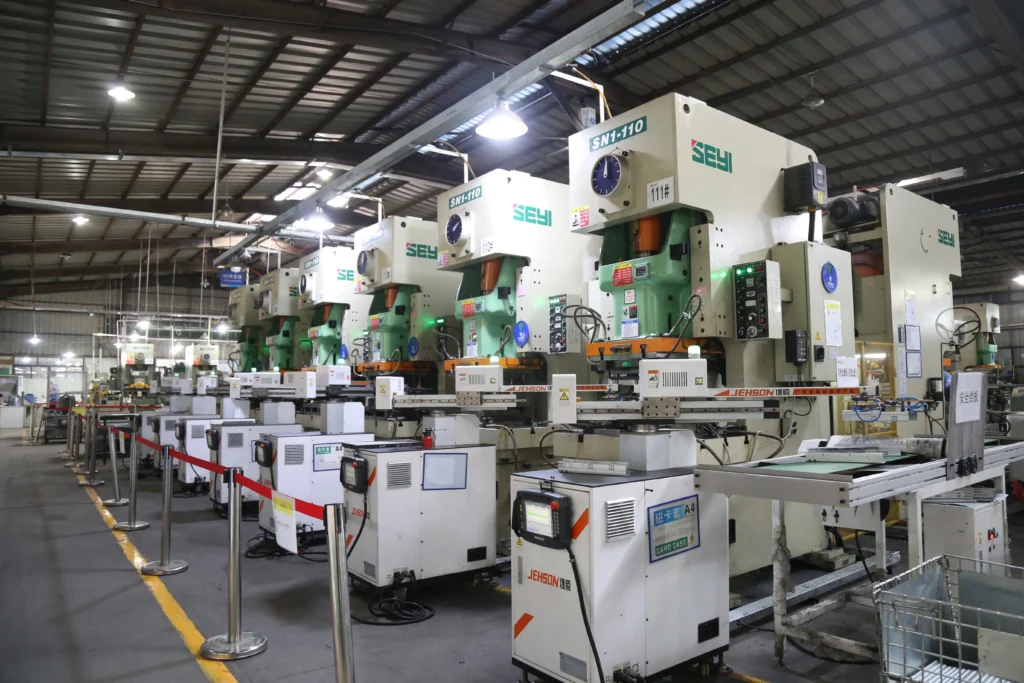
However, Jehson robots are not content with this. We understand that even an increase in efficiency by one stroke per minute can bring immense economic benefits to enterprises over time. Therefore, without changing the original production line process and molds, Jehson robots strive for excellence by focusing on the development of a new product—a small standalone punching manipulator—to further increase efficiency by 2 strokes per minute, reaching 14 strokes per minute (with a production output per minute of the line reaching 28 pieces).
The small standalone punching manipulator by Jehson is equipped with a transfer positioning assembly, which can position slide rails of different lengths to adjust the center position of the positioning slide rail. This ensures that the post-feeding arm always grips the center of the slide rail and accurately places it into the mold, guaranteeing precise mold punching. Therefore, it has excellent compatibility, flexibility, low mold requirements, and can adapt to the production of different slide rail lengths, demonstrating superior flexibility.