The rice cooker, as one of the indispensable daily household appliances, has made its way into thousands of households, and in recent years, its market demand has remained high, exhibiting a consistently growing trend. According to China Report Network, global sales of rice cookers amounted to 300 million units in 2017, with a production value reaching 70 billion yuan. As an essential kitchen tool in every household, the rice cooker market is immense yet faces a bottleneck in industrial growth.
Market Demand
Rice Cooker Sales in China: 300 Million Rice Cookers Sold Globally in 2017, Worth 70 Billion Yuan (chinabgao.com)
Rice Cooker Manufacturing Base: The production bases of rice cookers are mainly concentrated in Guangdong, Zhejiang and Shanghai, and these regions show significant advantages of industrial agglomeration development, with the total output of the three regions occupying 98.55% of China.
Rice Cooker Production Staff: The workforce involved in the production of rice cookers comprises approximately 50,000 individuals engaged in stamping operations. These jobs are often characterized by monotony and tedium, with a high incidence of work-related injuries and exposure to noise hazards. Additionally, the diminishing demographic dividend poses challenges to this labor-intensive sector.
Status of Rice Cooker Production lines: The mold technology employed lags behind, and the utilization of imported robots is costly and inefficient, unable to meet the annual growth rate of 20%.
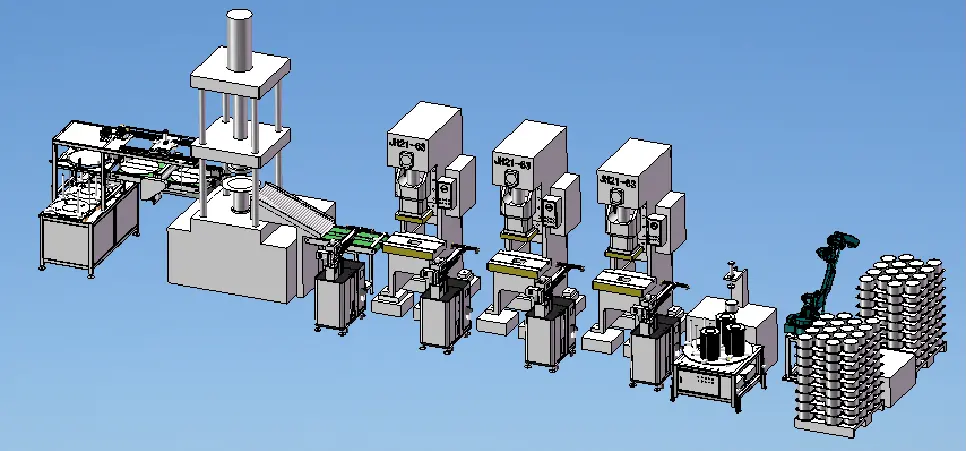
Pain Points of Traditional Production
Labor-Intensive Process: The entire production line requires at least 19 workers, indicating a high level of manual involvement. The production line lacks compactness and coordination, resulting in low automation. This heavy reliance on manual labor not only increases operational costs but also affects production efficiency and consistency.
Complex Mold Technology Leading to Waste: The complexity of the mold technology results in mold wastage. Specifically, the production of all holes in the outer shell necessitates the use of five side-punching molds, which directly increases the investment in labor, equipment, and molds. This complexity not only raises production costs but also prolongs the production cycle and reduces flexibility in adapting to product changes.
To overcome these challenges, it is crucial to explore automation and lean manufacturing techniques to streamline the production process, reduce labor intensity, and improve production efficiency. Additionally, optimizing mold design and manufacturing processes can minimize waste and reduce costs associated with molds, equipment, and labor.
Innovative Solutions
With the advantages of “turnkey” service of stamping molds, robots and system integration, we provide a set of fully automated and unmanned intelligent robot production line suitable for rice cooker from raw material sheet through servo sheet feeder to realize automatic oiling, stretching and loading, and then through the swinging-arm robot to flexible connecting multi-channel stamping and forming equipment, and finally through the palletizing robot to complete the stacking, Robot production line.
New Process 1: 0ptimize and merge the mold process, reduce equipment investment; through the mold intelligent quick-change and the robot inside and outside, realize the small batch diversified fast and flexible production.
Bottom of the mold process source, optimization and merger of the traditional 5 process side punching for 1 process, greatly reducing the customer punching machine, mold investment and valuable space on the scene; at the same time, the use of quick-change insert mold structure, to achieve online quick-change to meet the production line can be flexible production of multiple categories of models to meet the production line, reducing the customer’s investment in molds, and at the same time, lay the groundwork for rapid customized production of small quantities.
New Process 2: Automatic loading and unloading at the first and last stations, and fully autonomous robot stamping and forming in the middle,replacing imports and reducing costs.
By matching the servo sheet feeder for automatic feeding and greasing of rice cooker sheets at the first and last stations respectively, and the palatalizing robot for stacking of finished nice cooker product is off the line, and utilizing the central control system that integrates the servo sheet feeder,stamping robot, palletizing robot and is reserved for the expansion of the AGV unmanned cart,ERP and other system modules,we can realize the unmanned production line of intelligent robots for rice cooker – laying a solid foundation for the inteligent factory under the environment of industry 4.0.
New Process 3: Integration of industrial internet and manufacturing execution system, connecting people, equipment and materials, real-time monitoring and control, and creating a digital smart factory.
The management and control technology between MES system and robot controller records the production data of stamping equipment and robot in real time and accurately without anyone’s participation, realizing remote monitoring of stamping process, remote after-sales service and maintenance of stamping robot, and digital management of stamping workshop. It effectively improves the application and management level of stamping workshop. It runs more smoothly and stably, and meets the intelligent production elements of robots in the environment of Industry 4.0.
Before Upgrade | After Upgrade | Result | |
Workers | Quantity of Workers: 19*3-shifts=57 workers Annual Salary Expenditure: 57 workers*$5000*12 months=$3.42 million Annual Production Capacity: 5 pieces/minute × 60 minutes × 24H × 365 days ≈ 2.628 million pieces | Quantity of Workers: 1*3-shifts=3 workers Annual Salary Expenditure: 3 workers*$5000*12 months=$180,000 Annual Production Capacity: 12 pieces/minute × 60 minutes × 24H × 365 days ≈ 5.256 million | Reduction of labor costs by 20 times Increase in annual production by 2 times |
Equipment | 1 forklift (with labour) standby for mold changing Punching machine utilization rate 70% | Quick-change insert mold structure, to achieve online quick mold change Punching machine utilization rate 95% | Increased utilization rate of 25% 3.3 times less mold cost |
Material (molds) | 2 sets *5 processes =10 sets Mold cost $1 million | 1 set * 5 processes=5 sets Mold cost $300,000 | |
Method | Series of personnel management systems, such as attendance, performance, safety and security | Take care of the machine only | Automation, Intelligence, Informatization, Leanness |
Environment | Crowded, forklift rampage, mold preparation occupies space, site chaos | The workshop is neat and tidy, more like an exhibition hall |
Explicit Benefits
- annual profit increase: 5.256 million pieces- 2.628 million pieces=2.628 million piece*$1=$2.628 million (set the work-piece profit calculated at $1/piece)
- Increase revenue: profit increase + labor savings + mold savings = $3.15 million + ($3.42 million – $180,000) +$ 2.628 million≈ $5.868 million
Hidden Benefits
Quality, safety and absolute security advantages, will not be product quality, workplace accidents and employee management headaches.
Derivatives
This production line has been successfully imported into many domestic rice cooker brands such as Midea, Rongsheng, Huaqiang, providing a model project for the huge domestic rice cooker market. This line provides a standard for the typical “loading, oiling, stretching, stamping, palletizing” process in the stamping industry, which has strong industry universality, replicability and popularization significance. The core product of this production line, swing-arm intelligent stamping robot, will gradually replace manual feeding and become a highlight of the stamping industry, and will drive the rapid development of the stamping industry.