Leveraging Jehson’s expertise as a national specialized and innovative “little giant” enterprise in the smart stamping segment, we provide optimal mold automation or various robot integration methods tailored to different mold processes and procedures for the smart stamping of air conditioner outdoor unit components such as left and right side panels, cover plates, top covers, front panels, and electrical cover plates. We balance low-cost investment with high efficiency and high benefits.
“Swing-Arm” Robot Stamping Line for Air Conditioner Left Side Panel
Process Flow: Operators manually place sheet material on the servo sheet decoiler → The decoiler’s arm grabs the sheet for secondary positioning → The swing-arm robot picks up the positioned sheet and places it in Punch Press 1 for stamping → The robot retrieves the stamped product and proceeds to Punch Press 2 → The robot continues to Pick up and process through Punch Press 3 → Punch Press 4 → Punch Press 5 → Finally, the robot places the finished product onto the conveyor belt for discharge.
Robot Cycle Time: Approximately 10-12 pieces/minute.
Our Provided Equipment: 6 four-axis swing-arm stamping robots + 1 servo sheet decoiler + 1 conveyor belt for discharge.
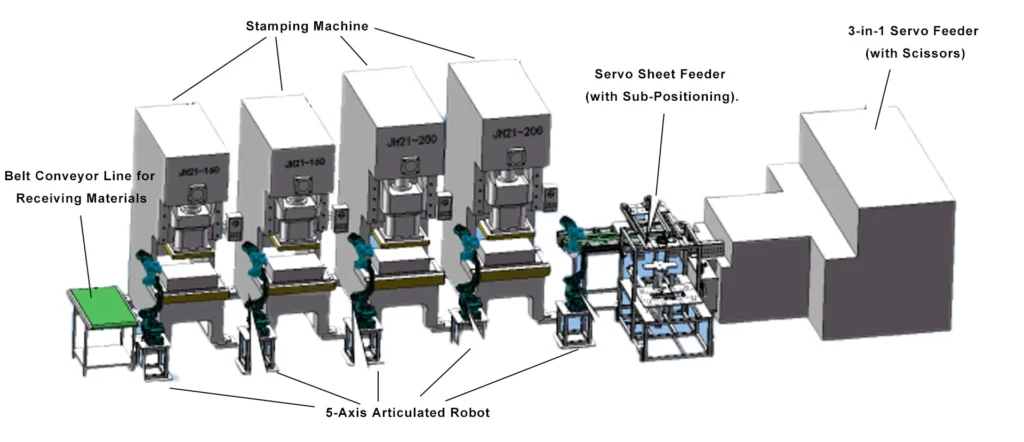
“Articulated” Robot Stamping Line for Air Conditioner Right Side Panel
Process Flow: Sheet material is fed by the servo sheet feeder → Grabbed by a 5-axis articulated robot → Punched in Punch Press 1 → Grabbed again by the robot and moved to Punch Press 2 → Repeated through Punch Press 3 → Punch Press 4 → Finally, the robot places the product onto the conveyor belt for discharge.
Robot Cycle Time: Approximately 7-9 pieces/minute.
Our Provided Equipment: 1 conveyor belt + 1 servo sheet feeder + 5 five-axis articulated robots + 1 three-in-one servo feeder.
“Standalone” Robot Stamping Line for Air Conditioner Top Cover
Process Flow: Sheet material is fed from the three-in-one feeder to the positioning conveyor → The conveyor positions the sheet → A standalone manipulator grabs the positioned sheet from the conveyor → Punched in Punch Press 1 → Grabbed by the manipulator and moved to Punch Press 2 → Repeated through Punch Press 3 → Punch Press 4 → Punch Press 5 → Then to the bending machine → Finally, the manipulator places the product onto the conveyor belt for discharge.
Robot Cycle Time: Approximately 10-12 pieces/minute.
Our Provided Equipment: 6 standalone stamping manipulators + 1 three-in-one feeder + 1 bending machine + 1 positioning conveyor + 1 conveyor belt for discharge.
“Articulated” Robot Stamping Line for Air Conditioner Front Panel
Process Flow: Sheet material is fed from the three-in-one feeder → Grabbed by an articulated robot → Punched in Punch Press 1 → Grabbed again by the robot and moved to Punch Press 2 → Repeated through Punch Press 3 → Punch Press 4 → Punch Press 5 → Finally, the robot places the product onto the conveyor belt for discharge.
Robot Cycle Time: Approximately 7-9 pieces/minute.
Our Provided Equipment: 6 articulated stamping manipulators + 1 three-in-one servo feeder + 1 conveyor belt for discharge.
Automatic Stamping Line for Air Conditioner Outdoor Unit Base Plate (Progressive Die + Three-in-One Feeder)
For the smart production line solution for air conditioner outdoor unit base plates, we utilize a combination of progressive dies and a three-in-one servo feeder. Through the feeder’s leveling and servo conveying functions, raw materials are automatically loaded. Progressive dies allow for multiple processes to be performed in a single die set, enabling rapid continuous production, significantly enhancing productivity, and reducing costs. These intelligent manufacturing solutions for air conditioner exterior components fully demonstrate Jehson’s robust capabilities in smart manufacturing support across the entire home appliance industry chain.