By thoroughly analyzing the traditional manufacturing processes and procedures of disinfection cabinets, we have leveraged our company’s full industrial ecosystem advantages in sheet metal processing, mold-making, robotics, and intelligent manufacturing. From pioneering the development of disinfection cabinets to mold design and manufacturing, and further to automated stamping, welding, assembly, packaging, and logistics warehousing, we have successfully developed a fully automated flexible stamping and assembly production line tailored for large-scale personalized customization of disinfection cabinets.
Core Innovations
- Adopting Adjustable Intelligent Mold Conversion: In conjunction with highly efficient, in-house interconnected robotic arms, we achieve rapid and flexible production of sheet metal cabinets for disinfection cabinets of various capacities online. This addresses the demands for personalized product customization from the source.
- Utilizing Virtual Axis Technology: By establishing digital twin models, we ensure coordinated and efficient motion control among robots, standardized equipment, non-standard equipment, inspection equipment, and other robotic devices related to the final assembly line. Artificial intelligence is also integrated into defect detection, screwdriving, and visual positioning for welding robots, enabling machine learning and decision-making.
- Based on the Central Control, Industrial Internet, MES, and CPS Physical Information Systems: These systems connect personnel, equipment, and materials, enabling real-time monitoring of production processes, intelligent scheduling, and material management. This establishes a fully connected manufacturing information platform on the industrial internet.
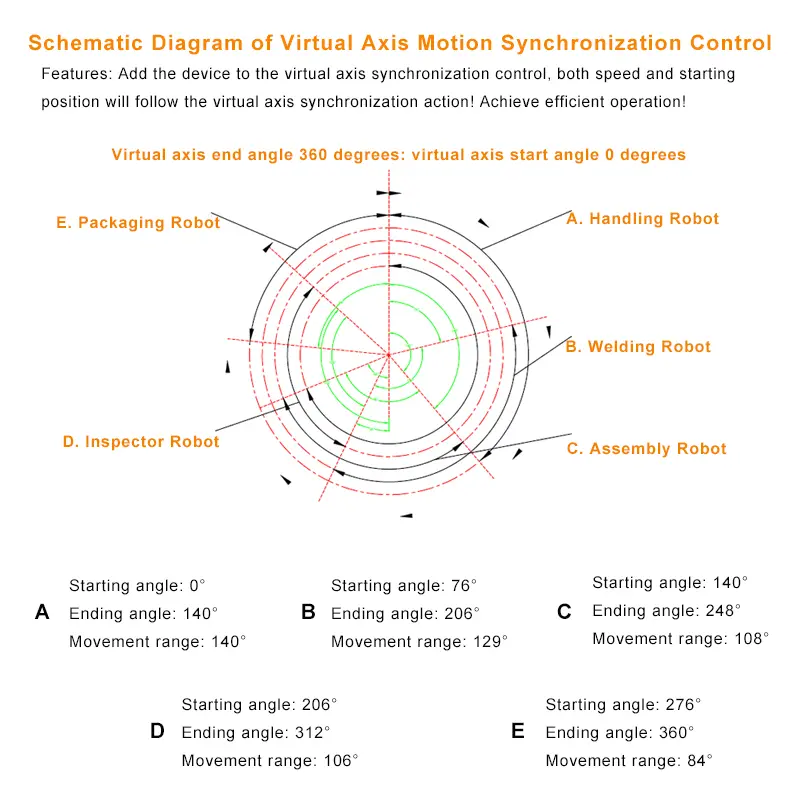
Advantages
- Process Advantages: We have modularized and standardized the process design for the seven major components of disinfection cabinets (heating tube, left and right side panels, front panel, aluminum strip with sealing ring, PCB circuit board, shelf, and upper and lower cover plates), significantly enhancing assembly efficiency.
- Equipment Advantages: The project includes 48 pieces of equipment, comprising 10 specialized machines, 3 stamping robotic arms, 23 6-axis articulated robots, and 12 sets of sheet metal molds. All are independently developed and produced by our company, and have been standardized to replace imports, reducing costs and increasing efficiency.
- Integration Advantages: There is horizontal integration from pioneering disinfection cabinet product development to mold design and manufacturing, through to robotic stamping, welding, assembly, inspection, and packaging.
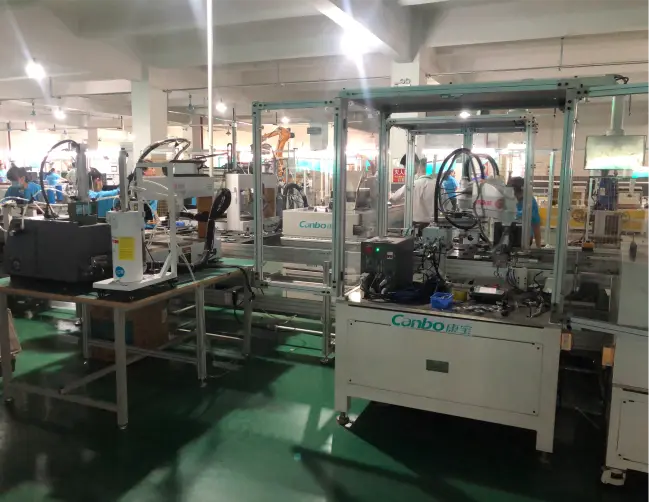
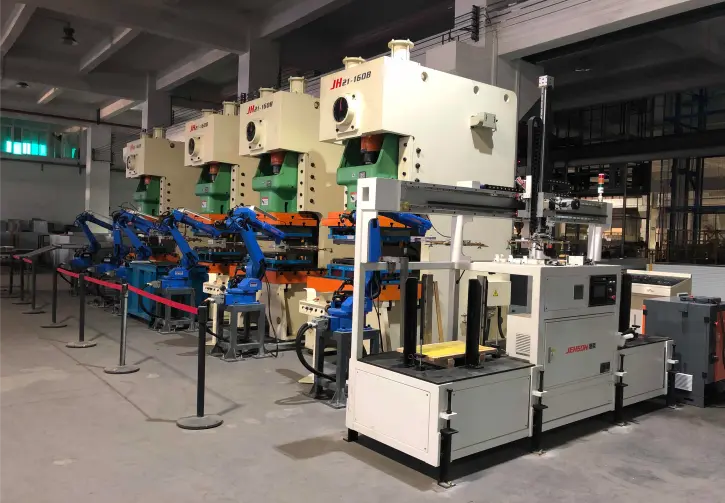
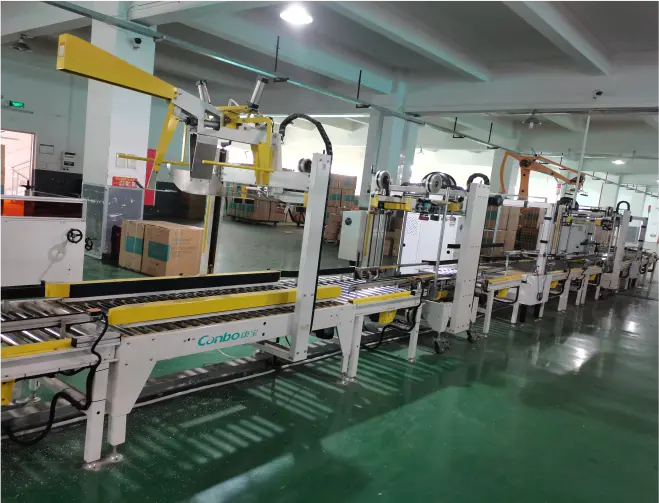
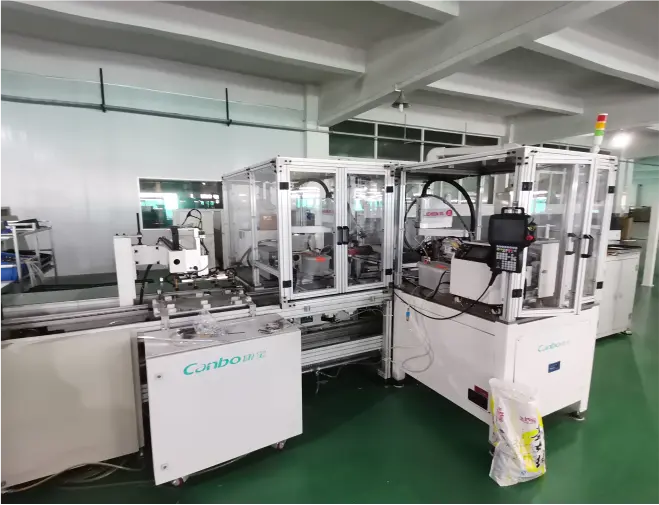
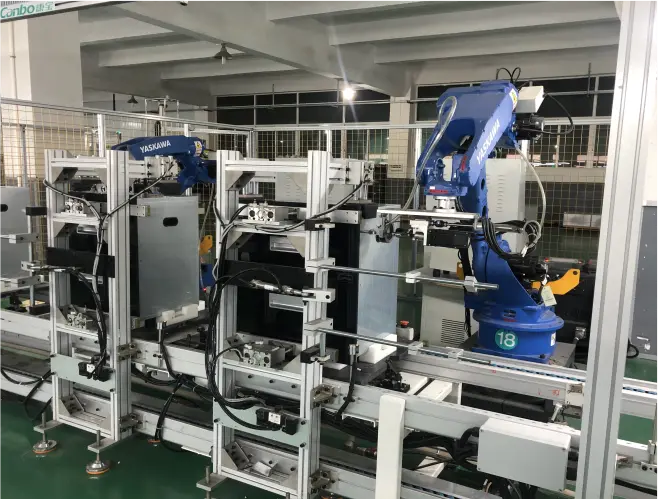
This project has been successfully implemented in the embedded disinfection cabinets of Kangbao, a leading domestic manufacturer of disinfection cabinets. It serves as a model project for the vast domestic disinfection cabinet market. It provides a standard for the typical “stamping → welding → assembly → inspection → packaging” process in the healthy appliance industry. It boasts strong industry versatility, reproducibility, and promotional significance. After implementation, the workforce was reduced from 95 to 27 individuals, while production volume increased from 550 to 1,000 units, demonstrating significant economic and social benefits.