This project realizes the highly automated and flexible production processes for the thermal fitting of compressor stators and housings, the press-fitting assembly of rotors and pump bodies, as well as online inspection during pump assembly.
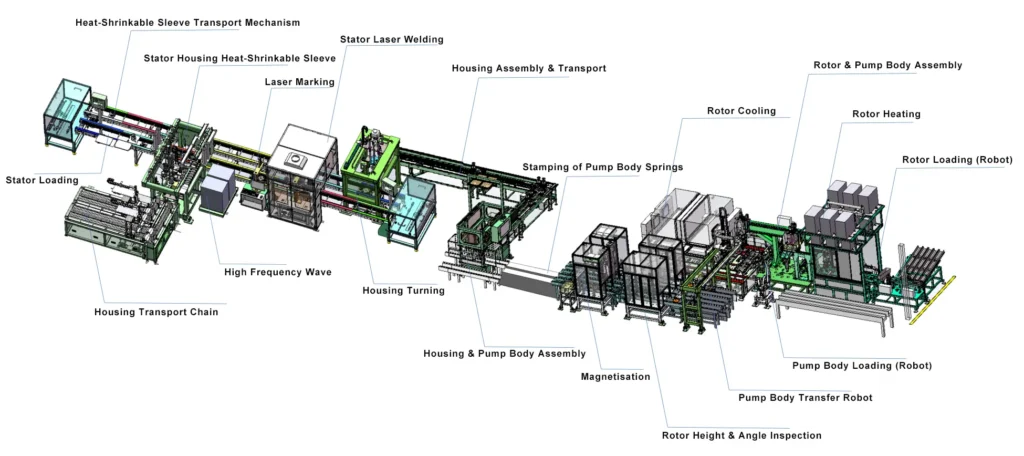
Innovation
Innovative Process 1: Core equipment for stator-housing thermal fitting, rotor-pump body thermal fitting, and housing-rotor-pump body press-fitting has been developed, forming a fully automated assembly line.
Innovative Process 2: By incorporating two sets of lifting magnetizing mechanisms, convenience and assembly efficiency are enhanced. Step-by-step heating further improves processing quality.
Innovative Process 3: Utilizing a vision system and robots, the circumferential position of the housing is precisely adjusted, ensuring the reliability of the housing-rotor-pump body press-fitting.
Equipment included: Housing Thermal Fitting Machine, Stator Laser Welding Machine, Thermal Fitting Material Feeding Machine, Rotor Thermal Fitting Pump Body Cooling Oven, and Online Magnetizing Machine.
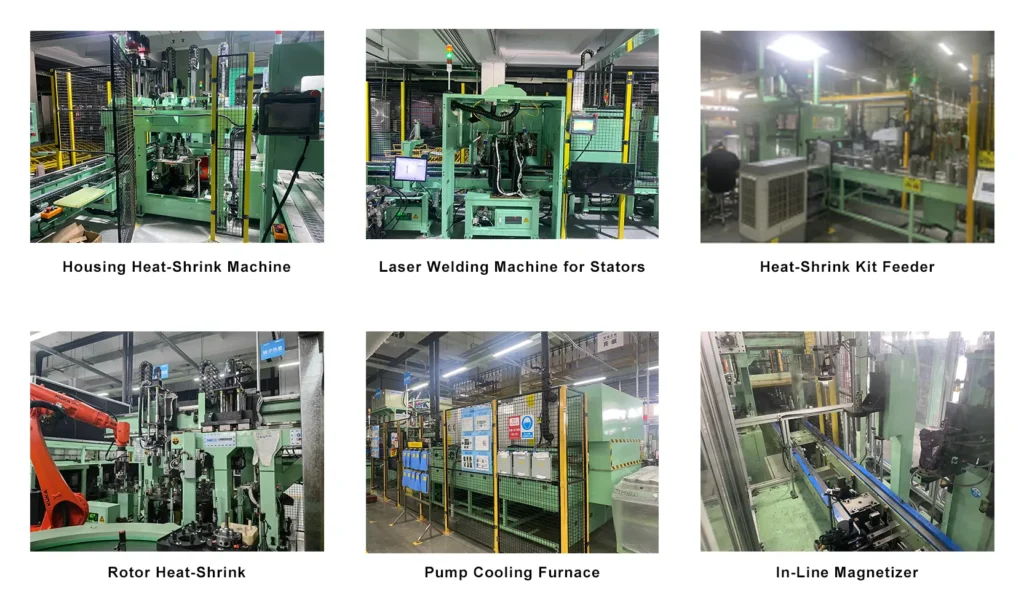
Implementation Effects
The workforce has been reduced from 20 individuals to just 2, while production output has increased from 4 units per minute to 10. Model changeover time has also been shortened from over 2 hours to just 5 minutes.
Product Honors: Granted 4 invention patents.