The washing machine cabinet, with its maximum height exceeding 1.5 meters and weight reaching up to 20 kilograms, is typically produced through a four-step process involving a 400-ton heavy-duty press machine in conjunction with molds. This traditional manufacturing process presents two major pain points. Firstly, since the washing machine models are differentiated based on cabinet size, each model necessitates a unique set of molds, thereby escalating costs, occupying valuable production space, and causing significant inconvenience during mold changes on the production line. Secondly, the large spacing of 6 meters between consecutive heavy-duty press machines, coupled with the cumbersome size and weight of the cabinet sheet metal, necessitates a total workforce of 20 individuals per line, resulting in extremely low efficiency and frequent workplace injuries. This has become a quintessential labor-intensive production line.
Traditional Manufacturing Process and Its Pain Points
The traditional process relies on two sets of molds, with manual mold changes and material feeding to produce two different specifications of components. This approach entails increased mold costs, space utilization, time-consuming efforts, high accident rates, and inefficiencies.
Overall Improvement Plan
The solution includes integrating one secondary positioning station, four independent stamping robotic arms, three articulated robots, seven waste material conveyor belts, two product conveyor belts, one riveting mold with feeding device (excluding the hydraulic press), and two single-station sheet metal feeders. This setup facilitates a fully automated production workflow, encompassing automatic feeding of raw materials for washing machine cabinets, stretching, stamping, waste collection (including scraps), riveting, and stacking.
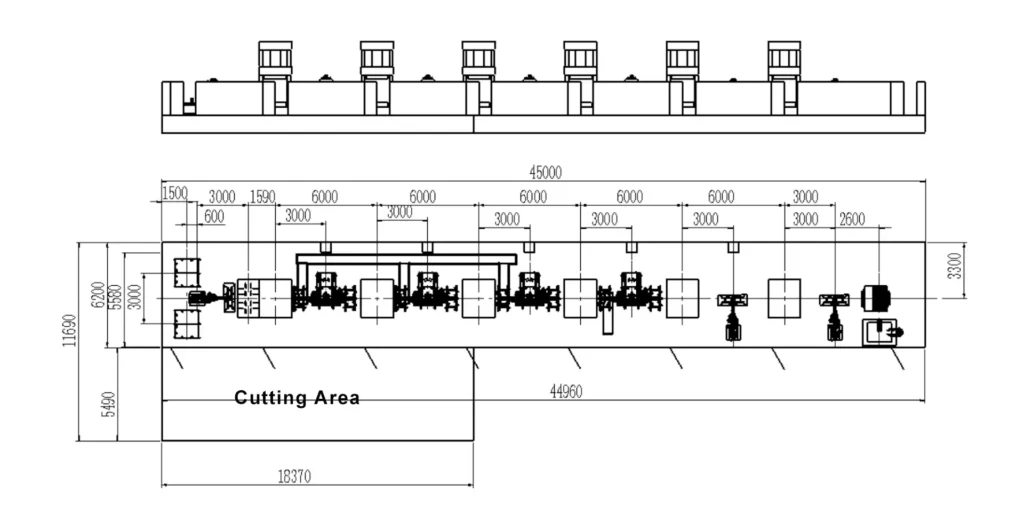
New Process Innovations
Mold Improvement: Intelligent Adjustable Quick-Change Mold Technology
We have autonomously developed a simple and rational mold design that meets the needs of producing two different specifications of components with a single mold, addressing an industry gap and aligning with energy conservation and emission reduction objectives. This mold leverages PLC-controlled cylinders for mold changing, ensuring intelligence and environmental friendliness. In practical applications, it seamlessly integrates with independent robot hardware and software, achieving a high level of intelligence and automation.
Automation Improvement: Large Sheet Metal Stamping Independent Robotic Production Line
This production line is suited for large sheet metal components, offering extensive grasping capabilities and multi-directional rapid flexible production, including left-right, up-down, and turning movements. It can replace imported robots, reducing costs by 50% and increasing efficiency by 60%.
Input-Output Analysis
Explicit Benefits
- Annual Profit Increase: Approximately 315 million pcs – 157.5 million pcs (assuming double production efficiency) × ¥1/piece ≈ ¥157.5 million(assuming a profit of ¥1/pcs).
- Additional Income: Total increase in income equals profit increase plus labor cost savings plus mold cost savings = ¥157.5 million+(¥360 million- ¥18 million) + ¥150 million≈ ¥650 million.
Implicit Benefits
It offers absolute advantages in terms of quality and safety, eliminating concerns related to product quality, workplace accidents, and employee management.
Before Upgrade | After Upgrade | Notes | |
People | Workforce: 20 people/shift * 3 shifts/day = 60 people/year Annual salary: 60 people * $5,000/month* 12 months = $360 million Annual production: 6 pcs/mins * 60 minutes/hr * 24 hrs/day * 365 days/year ≈ 315 million pcs | Workforce: 1 person/shift * 3 shifts/day = 3 people/year Annual salary: 3 people * $5,000 /month * 12 months = $18 million Annual production: 12 pcs/mins * 60 mins/hour * 24 hrs/day * 365 days/year ≈ 630 million pcs | Labor cost reduced by 20 times Annual production increased by 2 times |
Machines | Regular use of one forklift (with a driver) Press machine utilization rate: 70% | Press machine utilization rate: 95% | Utilization rate increased by 36% Mold cost reduced by 2 times |
Materials (Molds) | 2 sets * 5 processes = 10 molds Cost: ¥300 million | 1 set * 5 processes = 5 molds Cost: ¥150 million | |
Methods | Necessitates attendance, performance, safety precautions, and other regulatory frameworks | Requires only machine maintenance | Automation, intelligence, informatization, and lean management |
Environment | Crowded workforce, space occupied by molds, forklift traffic, messy and unsafe conditions | Workshop resembles an exhibition hall |